The following article deals with drying and filtration of compressed air, their great importance and impact on the efficiency of compressed air systems.
Liran Dayssi, EL-AV Compressors Ltd. April 4, 2021
In recent years, filtration and drying of compressed air have become an integral part of compressed air systems in industry.
This is due to the fact that most production machines now require clean dry air, to one degree or another.
Clean dry air equals money saved. Compressed air systems operating without an air drying and filtration system, or drying and filtration systems improperly maintained are given to higher wear—both to compressed air piping and consumers such as production machines and work tools—and operate at significantly lower efficiency.
Compressed air contains moisture as well as various contaminants, such as: dust particles, oil, bacteria and more.
Removal of the moisture requires the use of an air dryer. Removal of contaminants from compressed air requires the use of in-line filters of various filtration and flow rate degrees.
The standard applied for compressed air quality is ISO 8573. This standard defines the quality and/or purity of compressed air, and what is required in order to comply with its requirements. The standard is divided into nine different levels of quality, each with a definition of the amount of contaminants permitted according to the amount of particles per cubic meter, the amount of water, and the amount of oil (see table).
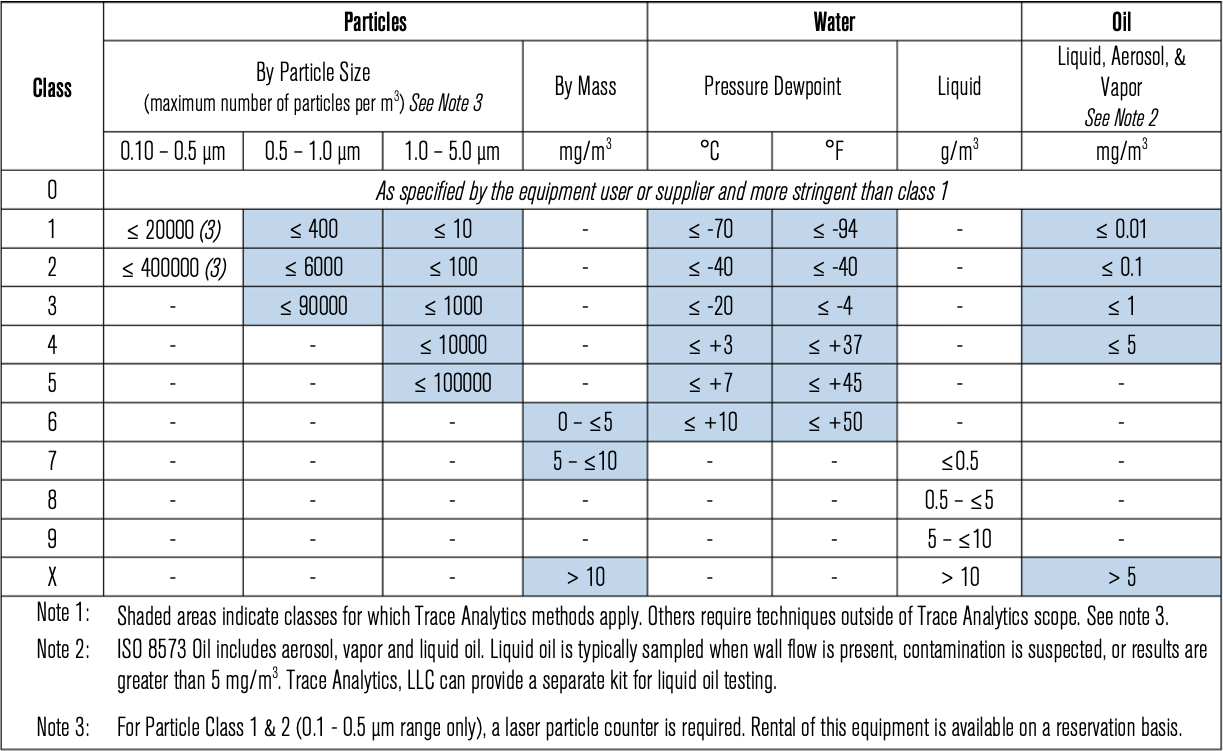
For air dryers there is a variety of technologies to serve different purposes, some of which we’ll discuss in the following.
The ability of an air dryer is measured by dew point, which simulates the condition of moisture at different temperatures.
Several terms related to moisture:
Relative moisture
Relative moisture is a percentage of the maximum moisture the air can carry at a given temperature and altitude (a certain barometric pressure).
For example, at a temperature of 77°F (25°C), at sea level, the air can contain up to 3.1% water vapor, at most.
Dew point
When air with a particular value of relative moisture is cooled it reaches a saturation temperature. At saturation, relative humidity reaches 100% of the air’s ability to carry moisture. Cooling the air beyond this point will cause the first dew point, and condensation of the water (or gas) vapor.
Chilling the air and condensing the liquids
Operation of compressed air systems causes significant heating of the air during compression. This increases the air’s ability to carry water vapor, or reduces the relative humidity in the air. When air cools, its ability to carry moisture diminishes.
Various air drying technologies
Refrigerated air dryers
These are the most common compressed air dryers, which usually operate at a dew point of 37.4°F (3°C).
Refrigerated dryers operate with a gas cooling system. Cold gas is transmitted into a heat exchanger, through which air is transmitted, simultaneously with the gas. The air is thus cooled, the dew point drops, and water vapor is condensed.
The condensed water descends to a low point in the heat exchanger, and from there drained out of the dryer by an automatic drain.
This technology is the most common and the most in demand in most industries.
In most cases, this technology satisfies the requirements of production machines and pneumatic work tools.
It is recommended to do a ‘house cleaning’ on this matter, and check whether the dryer in your possession is of new generation, to achieve better results and energy savings.
See explanation of refrigeration dryer technology in the following illustration:

Chemical adsorption dryers
Chemical adsorption dryers are suitable for working in environmental conditions under 32°F (0°C), medical applications, pharmaceuticals, electronics, and other applications requiring dry air at dew point below 32°F (0°C).
Adsorption dryers work with either natural or chemical adsorption material, such as silica gel, alumina, and zeolites.
The working principles of an adsorption dryer: The compressed air is passed through the chamber of the adsorption material for purification; after this, the purification cycle starts, at the end of which the air is transmitted to the plant air pipeline.
Several dryer methods exist, applied according to flow rate and air dryness requirements. The most common and widely used method is pressure swing adsorption (PSA). In this method there are two vessels containing adsorption material.
The compressed air is transmitted to Vessel A where it begins the drying cycle, at the end of which the air is transmitted to the plant air line, and some of it is transmitted through a purification valve (bypass) to Vessel B, in order to ‘cleanse’ it and prepare it for receiving compressed air to be dried; after this, a new cycle is started through Vessel B, and so on.
By this method, air at a dew point of -4°F to -94°F (-20°C to -70°C) is obtained. Although adsorption dryers provide dry air on a much higher level than refrigerated dryers, they are less energy efficient. This is because in order to perform the drying process they significantly increase air consumption, and thus increase energy consumption. Of course, these dryers exist in many different types. It is recommended to purchase the most efficient among them in order to significantly save electricity costs. The adsorption dryer’s effectiveness derives from the use of advanced control systems, as well as sophisticated valve systems. I would recommend that if a dryer on the level of an adsorption dryer is needed, to consult with a company specializing in them, in order to avoid malfunctions and unnecessary electricity costs.
Adsorption dryers are designed for applications with special air requirements. In most cases, a standard refrigeration dryer will meet the requirements, with no need for an adsorption dryer. Adsorption dryers are more expensive, and their energy efficiency is lower, resulting in higher electricity costs.
See the picture explaining the working principle of a pressure swing adsorption (PSA) dryer:
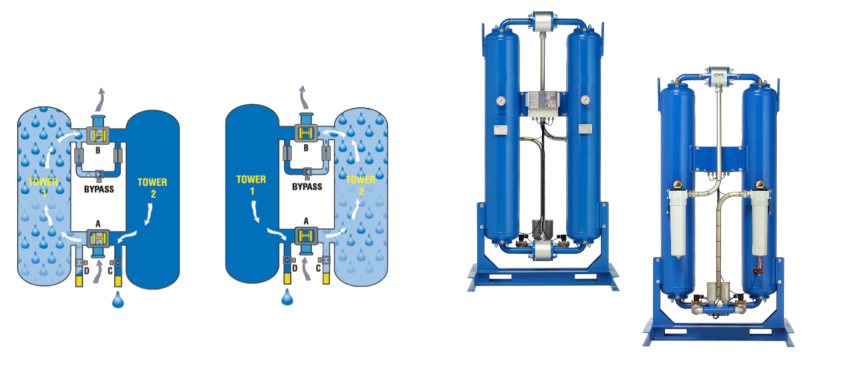
Air filtration and purification systems (lin-ine filtersו)
Compressed air is not clean; it carries various contaminants such as dust particles, oil particles, bacteria, etc.
Therefore, micron filters must be used to remove particles of various sizes, or anti-bacterial filters that filter bacteria out of the compressed air.
is necessary and required in a wide range of uses, such as: Painting, special machinery, equipment with high sensitivity to particles, medical uses, food, and more. Nevertheless, it is recommended that all users of compressed air, such as for pneumatic work tools and machinery, use in-line filters. Use of in-line filters maintains a clean air line, and this is worth money. When keeping an air line clean we prevent malfunctions in equipment, enable longer working life of production machines, prevent leaks from the air line, and of course improve the overall efficiency of the system as the result of a clean air line, with properly functioning air flow.

This might also interest you:
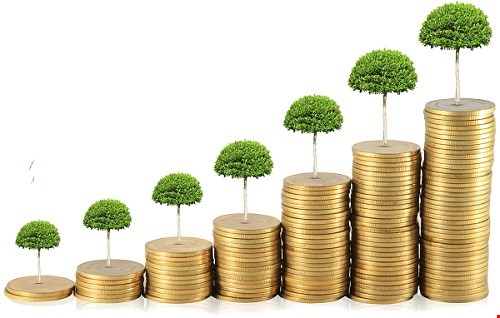
Energy Efficiency in Compressed Air Systems as a Tool for Operational Cost Savings
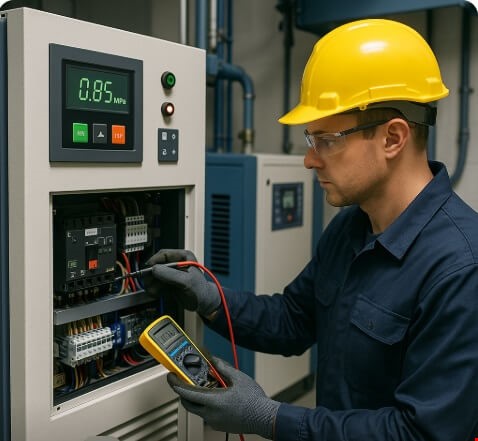
5 Common Industrial Air Compressor Problems & Solutions