What are the characteristics and advantages of a rotary screw air compressor? What is the difference between it and a piston compressor? What are the applications it is suited for?
Air compressors are a central component in automation-based industrial processes, and in a wide variety of jobs and tasks in the world of industry and crafts. Matching a compressor to its designated task is of critical importance. In the following paragraphs we shall present to you the rotary screw compressor, its working principle, its advantages, and the tasks to which it is suited.
What is a screw compressor?
An air compressor is a device that knows how to collect air from the atmosphere surrounding it and compress it into a designated vessel in order to create high-pressure compressed air. The most familiar version of air compressor is the piston compressor. The compressor’s work is based on a piston moving within a cylinder in order to draw air in, and compress it into the compression chamber. As opposed to the piston compressor, the screw compressor works in a totally different way. This compressor is based on two meshing helical screws with deep threads, revolving together in a male/female configuration within a designated cylinder. At the meeting point between the two screws, air from outside is compressed as rotation of the screws leads the air along the screws until its release into the oil separation tank at the screws’ other end.
What are the characteristics and advantages of a rotary screw air compressor?
The rotary screw compressor has several advantages over the piston compressor:
- Quiet and stable – the rotary screw compressor is considered very quiet and very stable compared to the piston compressor, since its action is in a single direction (rotation of the screws in one direction) and is therefore smooth, continuous, and free of vibration and rocking.
- High compression capability – the screw compressor has higher compression capability than the piston compressor. The reason for this is that the air pressure in the compression chamber creates direct resistance to the piston action whereas in the screw version, the motor’s power is channeled to turning the screws that move on a vertical axis towards the compressed air’s resistance. Resistance to the motor is smaller; hence, air can be compressed at higher pressures. These compressors usually come with motors anywhere from 5 to 500 horsepower, and are capable of creating maximum air pressure of 125 psi (larger models with multiple threads can reach 150 psi).
- Energy efficient – operation of a piston compressor is based on the motor shutting off when air pressure in the compressor reaches the required level, and restarting when it goes below a predetermined minimum. On the other hand, the continuous action of the rotary screw compressor enables its operation through an inverter device that maintains continuous operation of the motor, changing the motor’s rotation power according to changes in air pressure in the compressor. Thus, continuous compression, stable air pressure and significant savings in energy costs are achieved.
- High availability of compressed air – the constant action of the compressor at high compression power creates high availability of compressed air, even when demand for such air is high and continuous.
What applications are screw compressors suitable for?
Rotary-screw compressors are especially suited to industrial processes with the following characteristics.
- High work load – processes with high work loads and continuous demand for high air pressure, such as production lines in food plants and automatic production systems.
- Quiet work – processes that require quiet compressor work such as dental clinics and blood pressure measuring instruments. In small applications such as these, use is made mainly of a new generation of rotary-screw compressors based on a tapered (conical) thread that solves, to a large extent, the problem of air leakage during the compression process.
- Clean air – processes in which clean air is required such as pharmaceutical plants, microprocessor manufacturing, etc., since rotary-screw compressors can work with no oil at all or with mineral oils that are considered cleaner.
To conclude, screw compressors are especially suitable for industrial applications at high loads on the one hand, as well as clean and quiet applications on the other hand. This type of compressor enjoys several advantages at the core of a compressor’s functioning—air pressure level, vibrations, noise, availability of compressed air, and energy costs—and is without doubt considered a better alternative for the applications it is suited for.
This might also interest you:
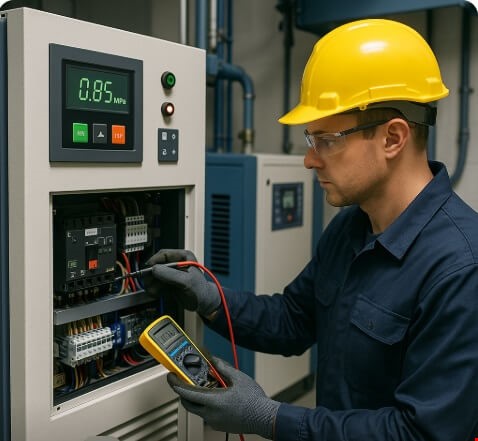
5 Common Industrial Air Compressor Problems & Solutions